Construction is a high-risk industry. That goes beyond the obvious safety risks on the jobsite to include financial risk as well. And even though there are a lot of different fields in construction, they share a few common pitfalls.
Here are the five most common mistakea that GCs and subcontractors encounter during the course of a project.
The 5 biggest mistakes for construction companies
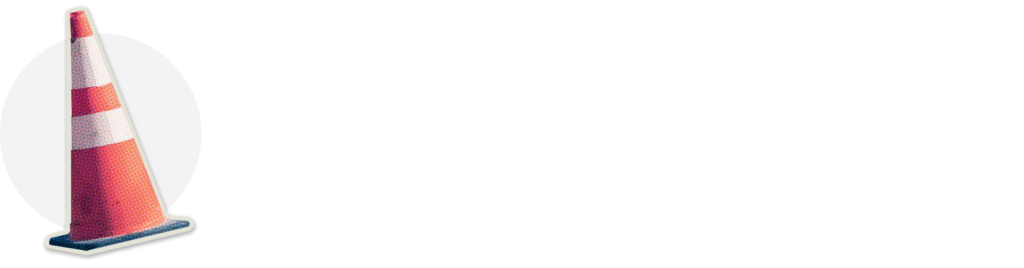
1. Sacrificing safety and quality
Deadlines. They hang over the heads of project managers, foremen, superintendents, and field workers like a heavy storm cloud. In an effort to meet these deadlines, workers may feel the need to cut corners and rush.
However, skipping over important safety protocols and best practices can lead to accidents and hazardous conditions on the jobsite, as well as shoddy craftsmanship that requires rework. Sometimes, the best way to get a job done quickly is to slow down and do it right the first time.
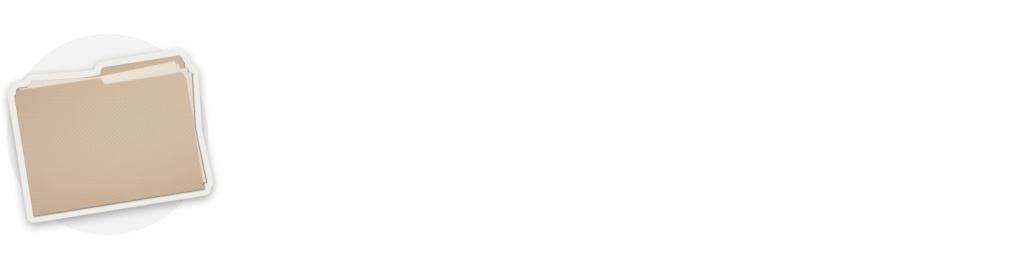
2. Relying on pen and paper daily reports
Sometimes, the biggest time sinks in construction don’t come from how long it takes to do the work, but how long it takes to record the work that’s already been done. Supervisors and foremen often spend hours a day just documenting what their employees are doing. Even then, pen and paper reports are easy to misread, leading to mistakes and inaccurate information down the road.
Not only that, but sharing these reports can be difficult, as can storing them. Plus, your ability to find these reports later on depends entirely on your coworker’s organizational skills. And that’s just better not left up to chance.
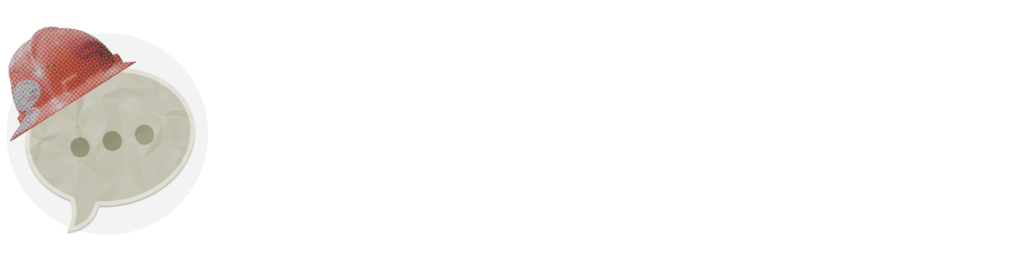
3. Not scheduling safety talks
Safety on the jobsite is important, both for employee wellbeing and for project timelines. Toolbox talks, also known as tailgate talks or tailgate meetings, are a great way to debrief crews on hazards they may encounter in their specific project.
By neglecting to schedule these talks, project managers may unintentionally be putting workers at risk. It doesn’t hurt to take a few minutes out of the day to cover relevant safety topics each day.
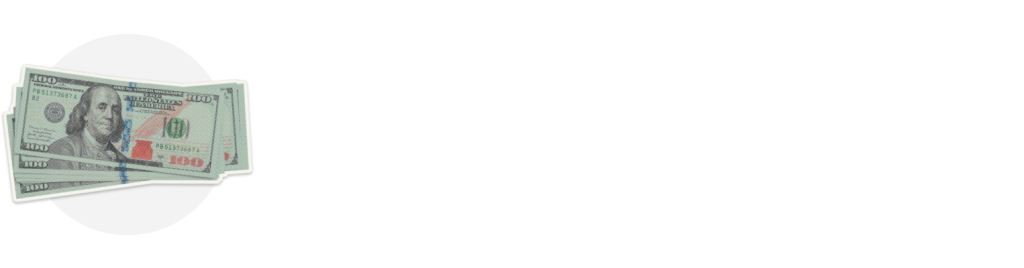
4. Poor budgeting
Few things cause a construction project to grind to a halt faster than insufficient funding. It can be hard to estimate how much a project will cost ahead of time, but failing to do so can make the difference between completed construction and a vacant lot.
All factors have to be considered in a construction budget, including equipment, materials, labor, and taxes. And a good budget should always include contingencies in case of unexpected costs down the road.
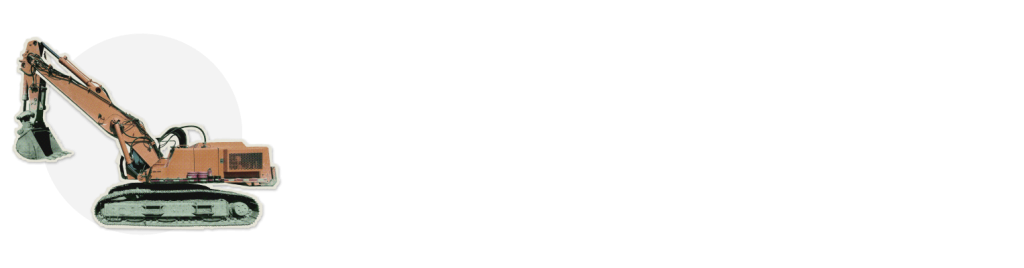
5. Inconsistent resource allocation
There are lots of moving parts on construction sites. And that doesn’t only include machinery. Workers also make or break a project, and are a company’s most important resource.
If a jobsite lacks the necessary equipment or skilled labor to complete a certain task, it can lead to delays that impact your scheduling and can push back your completion date. And, worst case scenario, it can lead to overpromising and under delivering on your projects.
How to avoid construction mistakes with Raken
Raken is your all-in-one digital tool for the field. We offer solutions that will proactively help you avoid these common pitfalls in your construction projects.
Our safety and quality dashboards and toolbox talks help you monitor safety on the jobsite and avoid common mistakes. And as far as unreliable pen and paper daily reports go, our digital daily reports are a great alternative. Not only are they easier to read (no more chicken scratch), but it's also more convenient to gather and share data in the field with mobile devices.
To avoid common budgeting pitfalls, it’s best to pair our own digital project management tools with reliable accounting software. Integrating the two is a great way to collect essential information and put it to good use for accurate budgeting.
Finally, our equipment and labor management tools help you work more efficiently. They’re a great way to stay on top of budgets and equipment maintenance, as well as track worker certifications and see how your skilled workers are distributed across projects.