The Old-Fashioned Way
In 2015, Rich DeLacy was about to start on one of the most complicated projects in his 20-year career with Hensel Phelps. He was the project superintendent for the Southwestern Yard Facility, a $173 million dollar build for the Los Angeles County Metropolitan Transportation Authority: 145,000-SF spread out over 18-acres with specialized maintenance facilities and equipment for servicing trains on 8 miles of newly-constructed light rail track built over 47 months.
A project with the size and complexity of the Southwestern Yard obviously comes with the reporting and documentation needs to match. Every subcontractor had to turn in a daily report, manhours had to be calculated, and photos and notes had to be stored and communicated with project stakeholders in a timely manner. What kind of organizational reporting system could handle the stress of so much documentation?
DeLacy knew that the old way just wouldn't hold up. "We'd typically use pen and paper and Excel. We'd provide a paper copy of a daily report to the subcontractors. They'd have to come in, take one out of the box, fill it out with their time and everything they had done that day, then come back in at the end of the day and turn that paper copy in," says DeLacy, noting "and then the field engineers would take all that information and manually fill it back into an Excel spreadsheet."
That process, while it might have worked in the past, definitely had numerous flaws that DeLacy pointed out. "Sometimes the project engineers couldn't read the subcontractor's handwriting," he says, continuing "but the biggest fight is the subs not turning their reports in, and the amount of follow-up you'd have to do just to get the paper copies from them. Instead of turning the reports in daily, you'd get a stack on Fridays, and sometimes the subs would leave without turning them in and you'd have to hunt them down on the next job. It was very painful."
Imagine that. A project engineer on a complicated site not only has to re-enter all the information from a paper daily report into an Excel spreadsheet, but right when everyone else is leaving the site getting ready to start their weekend on Friday they get a huge stack of backlogged daily reports that they then have to sit there and fill out.
Even on normal days, when the subcontractors were turning in the reports regularly, it was a huge drain on time and resources. "The engineers, depending on how many subcontractors we had at the time, could spend hours doing it," says DeLacy, "and we were upwards of 20-30 subs out here at our peak, so they could spend 2-3 hours a day manually re-entering daily reports into Excel."
A system that inefficient just wasn't going to hold up on a project like Southwestern Yard. Luckily, DeLacy had a goal of always trying out one new piece of technology on every project he's in charge of. And for the Southwestern Yard, he chose to use Raken.
“We were able to see substantial time savings just by using Raken. The engineers save a huge amount of time by having the subcontractors enter the reports themselves without having to re-enter it all.”
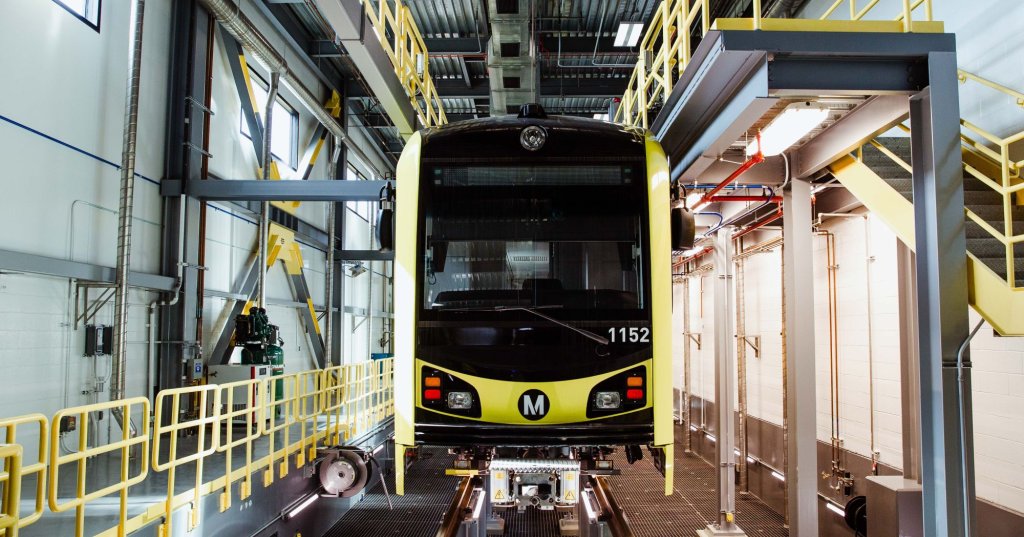
Raken Super Daily Saves (Hours In) the Day
DeLacy decided to use Raken on the Southwestern Yard project because he had heard it was the latest and greatest in field reporting construction technology out there, and it had one particular feature that he thought would make managing the Southwestern Yard project mountains easier. "I was interested in Raken initially because, at the time, the Super Daily was just coming out. With that, the subcontractors could sign up and fill out all their paperwork on their own," says DeLacy, noting "that meant I wouldn't have to redo all of it with the field engineers."
So DeLacy introduced Raken into his process. "We had all the subcontractors signed up for the Super Daily," he says, "and we used it to document where the job was at, and who was doing what."
One can easily see DeLacy's reasoning here: give the subcontractors the tool to enter their daily reports into a system on their own and take a time-consuming task out of the day at the same time. It should be a win-win, but the problem usually comes in getting the subcontractors to actually use the technology that you give them. Many aren't all that tech-savvy and, in the worst case scenario, you've bought software that no one uses so not only are you not making anyone's day easier, but you've wasted money doing essentially nothing.
That wasn't the case with Raken. Almost immediately, he saw a massive improvement in daily report compliance over the old pen and paper with an Excel spreadsheet process. "Once the subcontractors were onboard with Raken, it was very easy to get the dailies without much hassle," he says, "The ability for them to do the report on their phone means the subcontractors do them daily rather than wait until the end of the week and just give it to us in a stack on Fridays."
And what was the result of having the subcontractors use Raken to fill out and submit their daily reports? The time saving that DeLacy was hoping for. "We were able to see substantial time savings just by using it," he confirms, noting "The engineers save a huge amount of time by having the subcontractors enter the reports into Raken and not having to re-enter it all."
Because DeLacy and his team used a field-focused app to do their daily reports they were able to save the project engineers 2-3 hours every day. And it wasn't just the PE's that saw the benefits. "It's less time-consuming for the subcontractors as well," says DeLacy, "They aren't spending as much time filling out their reports and bringing them back." If you were to add up the 2-3 hours from every PE, as well as the time spent by the subcontractors in the field filling out the reports and then bringing them back to the office, it's no wonder that they were able to complete a huge project on time, under budget, and with all their documentation neatly wrapped up.
“The amount of time Raken saves our guys really contributes to their quality of life. They're not spending all their time in front of a computer. They can get in, get their daily reports done, and go see their families.”
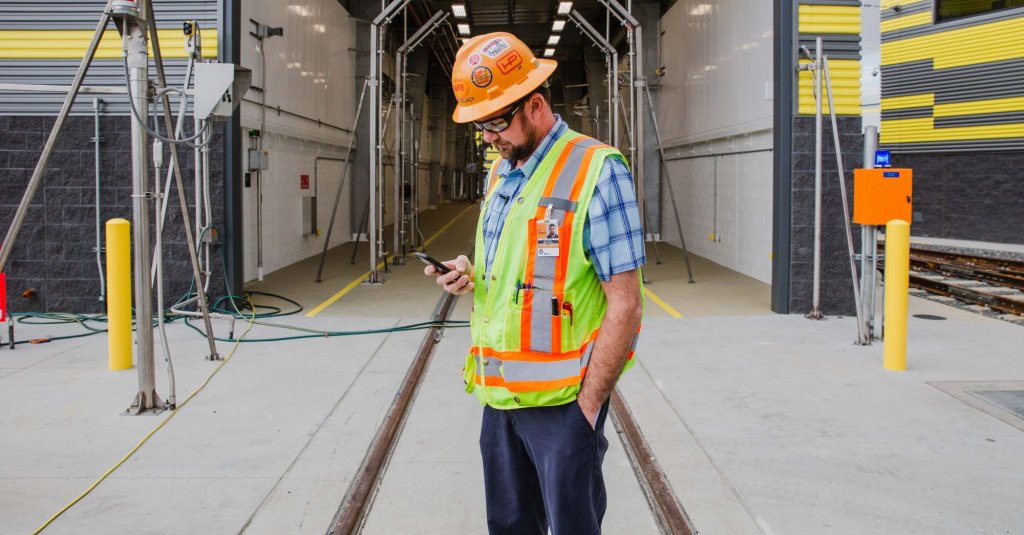
Ease of Use was the Key
So why were DeLacy and Hensel Phelps so successful with managing the documentation the Southwestern Yard project while so many other companies out there haven't quite gotten the hang of it? DeLacy has a theory, and it has to do with how easy the program you choose is. "We didn't have any complaints with Raken," DeLacy states, going on "the project engineers and subcontractors found Raken very easy to use. Talking to one of the subcontractors they said that the president of their company was very excited about Raken. He liked the way the reports looked, he had a source to see exactly where progress was at because the subcontractor was now taking pictures which Raken automatically included right at the top of the report. They all found it very easy and everyone was happy using it. In fact, many of the subcontractors have signed up with Raken on their own."
You might think that DeLacy just got lucky this time and was working with more open-minded, tech-savvy subcontractors, but that wasn't the case. "Even the more difficult subcontractors, the crusty old ironworkers, where usually it's difficult to get them on board with using technology, they were very receptive to Raken," he says, "we didn't have any problems getting all those guys signed up and using it."
Because the subcontractors found Raken easy to use they actually used it on a daily basis, meaning that for the first time DeLacy was able to get the documentation he needed without having to chase anyone down or waste hours re-entering it into a spreadsheet.
The best thing about Raken is the ease of the program, the fact that any subcontractor could do it on their phone," DeLacy says, "The talk to text, the pictures, and especially the rollover features were useful. Once the subcontractor had all their guys in Raken they just push a button and all the information roles over to the next day. Then all they had to do was put a quick description in there. So rather than sitting down and having to handwrite something, Raken's automatic features kept them doing their daily reports every single day.
Improving Quality of Life
So, by using a construction app focused on ease-of-use in the field DeLacy was able to save his PEs and subcontractors hours in their day and bring a complicated project home on time with all of the documentation in the right place without all the pain and headache of a pen and paper method. But that's not all the benefits he saw.
Beyond the amount of time Raken is saving, the reports themselves are higher quality," DeLacy says, "The way they look, and it's automatic. You aren't having to manually put in the pictures. And Raken automatically adds up all the man hours to date, so you have a one-stop shop where you can just open up the latest and greatest report and see exactly how many man-hours you've spent to date, as opposed to going into Excel and making sure that everything is updated the old-fashioned way.
But there was one more benefit that DeLacy saw after using Raken on the Southwestern Yard project. It was harder to measure, but far more valuable for the Hensel Phelps employees working there. "The amount of time Raken saves our guys really contributes to their quality of life," DeLacy notes, "They're not spending all their time in front of a computer. They can get in, get their daily reports done, and go see their families."
We couldn't have asked for a better outcome for DeLacy and his team: it's why we built Raken in the first place.
To find out more about the Southwestern Yard project, be sure to check out Hensel Phelps and their list of amazing, nationwide construction projects. Or, you can see even more construction app success stories and discover how more companies saved their crews time and stress with Raken.