The Problem: Maintaining Accurate Historical Data
As one of the largest mechanical contractors in the Northeastern US, inconsistent paper reports and spreadsheets—and varying metrics among project managers—made tracking projects difficult for J.W. Danforth. They needed a less manual way to assess the status of labor and productivity on their projects.
The Solution: Tracking Productivity in Real Time
With Raken’s real-time production insights, Danforth can track their progress (and make better decisions) faster. More reliable data also makes comparing estimated productivity and actual productivity easier than ever. This helps Danforth protect their business from potential losses by being able to direct additional support to their Field leaders in a timely fashion when issues arise, and can stay focused on the specific work tasks of concern.
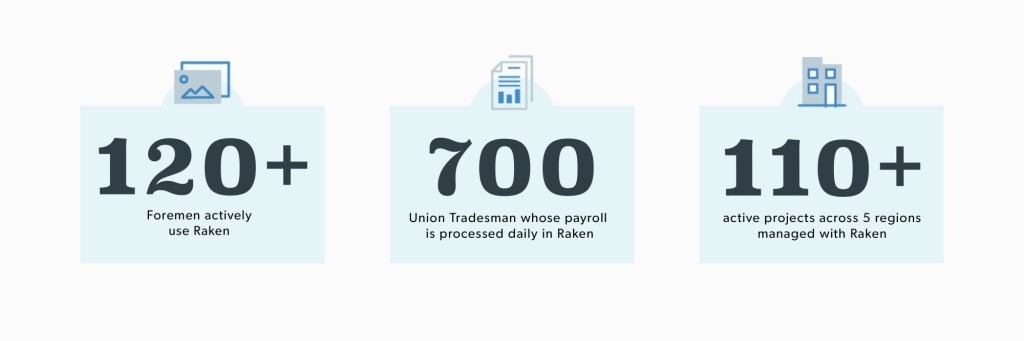
Making Better Decisions with Real-Time Production Insights
With well over 120 projects at any given time, Danforth needed more visibility into how each jobsite was doing. Before, they’d have to wait until after a job was completed to analyze their actual performance versus an estimate. Now, Raken gives Danforth real-time visibility into their labor productivity. That way, they can see how efficiently they’re working. And make decisions on the fly to do even better.
“If we have a bad week on a labor code, we’ll see the projected productivity start to drift away from the budget,” said Todd Follis, Danforth’s Vice President of Pre-Construction Planning. “Most people who don’t have this level of insight will just keep on doing the same thing again and again until someone sees it on a financial statement … and by then, it’s too late.”
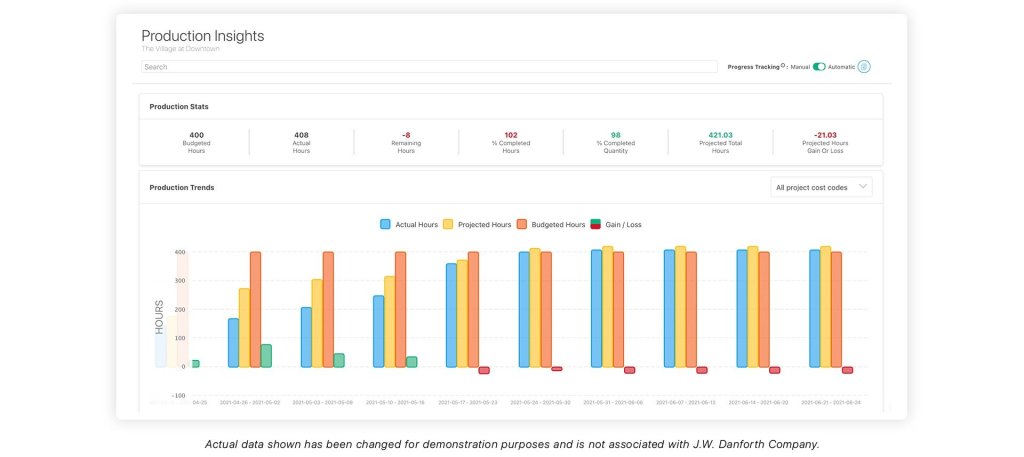
“Now, with the whole measured mile readily available and documentable, you know when you’re doing well and can share the reasons for success with other projects. You can also resolve poor performance effectively, and if it’s caused by others, demonstrate that to be compensated fairly,” Follis said.
Raken helps Danforth gather project data, and flag any labor codes of concern. From the software, Danforth can view the details of any labor code. Project managers can even see their performance trends over time. That makes it easy for Danforth to compare labor codes each week—and spot any problems or areas of improvement right away. Then, they can make changes in the field to improve productivity and meet their goals.
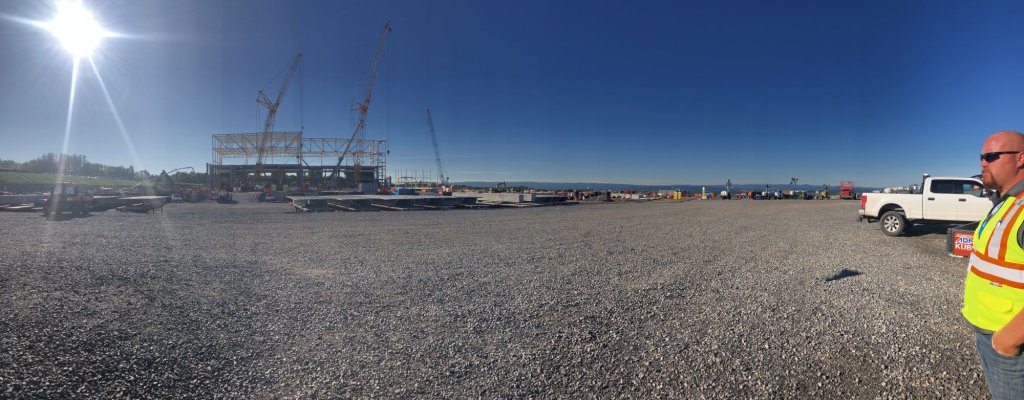
Using Standardized Data to Improve Visibility
Before Raken, Danforth didn’t have a uniform way to report estimates. Since every project manager would use different metrics, it was nearly impossible to compare estimates to their budgets (and each other). With production insights, Danforth standardized their reporting and could see everything at a glance.
“Now our data is standardized, so we can compare jobs, see what’s doing better and why, and communicate these facts across the organization so everyone can improve,” Follis said.
This real-time productivity data proved especially helpful during COVID-19. Danforth saw how much the pandemic was impacting their labor productivity—from project shutdowns to continuously changing safety protocols. Clean, accurate data helps them provide proof of additional costs, as well as who’s responsible for them.
“Everything with COVID-19 was an unplanned cost. But we’re able to show the impacts to labor and material, and we’re able to report that on a daily basis to the GCs and CMs, providing a real potential for fair and equitable compensation,” said Follis.
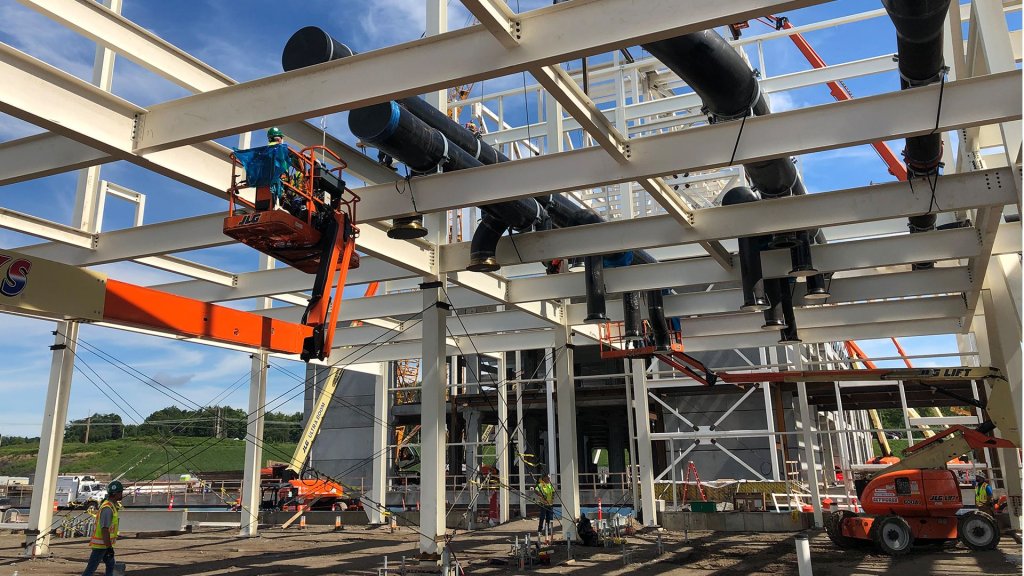
Defending Work During Disputes with Data and Time Stamps
Having solid, documented proof ensures your business stays protected during inevitable disputes. With your project data only a few clicks away, you can easily pull evidence to defend your work. Most recently, Danforth successfully defended requests for compensation for contract delays and productivity impacts with the federal government. And it’s all thanks to Raken’s digital data storage.
“The government wants to see accurate, time-based, meritable documentation. You can have all the facts, but without that daily first person corroboration from our field leaders doing the actual work, they question it,” said Follis.
Because Raken automatically time-stamped their daily logs, photos, and attachments, Danforth’s documentation supported their stated delays. This ultimately led to Danforth receiving equitable compensation.
“You don’t know what’s going to be important three months after you input it the day it happened,” Follis said. “But because everything’s time-stamped electronically, it’s proof we couldn’t have recreated or altered it.”
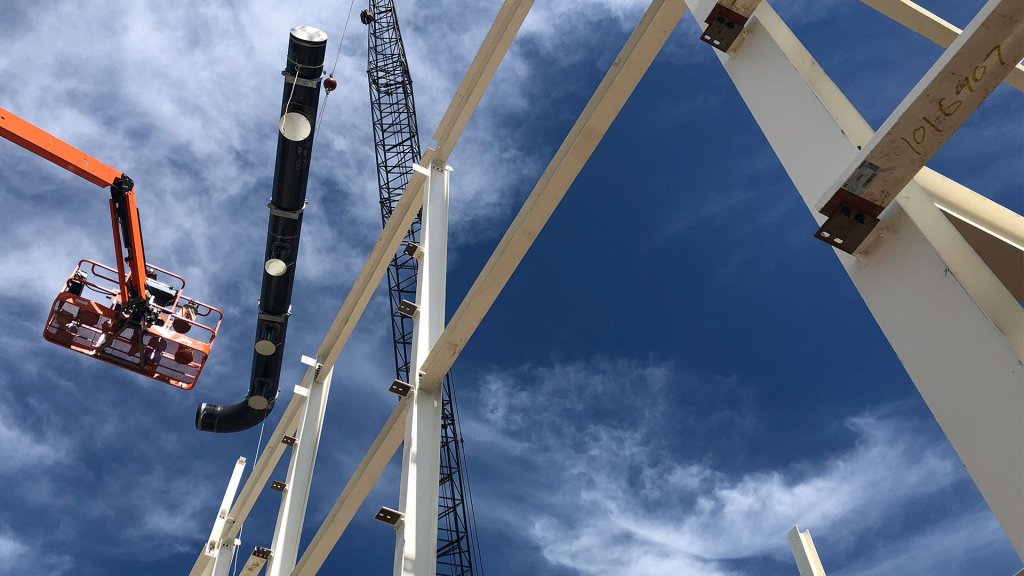
Improving Communication with Field-Friendly Software
To properly collect data that would give them better production insights, Danforth needed construction management software that was easy to use in the field and made communication easy. That way, there was less back-and-forth when it came to important project updates—and Danforth could act fast to stay on course.
“The most important thing we have is the power of our people, and Raken provides our field leaders with a clear and concise method of communication with management,” said Follis. “If we’re not listening to them, and can’t react to what their needs are, we’ve really missed the boat.”
Boost Your Productivity with Raken
With Raken, the John W. Danforth Company has a clean, digital record of all their project data. From time-stamped photos and attachments to production tracking, you can better protect your workers—and make better decisions faster.
Schedule a demo to see how you can improve your productivity with Raken's mechanical contractor software—just like Danforth. (It even comes with a free trial.)