In construction, how well a business manages assets directly affects productivity.
This guide will teach you best practices and introduce you to tools that maximize efficiency in your equipment management workflows.
What is construction equipment management?
Construction equipment management is a collection of strategies businesses use to keep track of owned and rental equipment. It includes processes for maintaining equipment, tracking the location of equipment, and scheduling equipment for use on the jobsite.
A construction company may refer to equipment management as fleet management or asset management.
A typical equipment management plan will focus on heavy machinery (like bulldozers, excavators, and forklifts) but may also cover light machinery and smaller tools.
A construction company may refer to equipment management as fleet management or asset management.
Why is construction equipment management important?
Construction equipment management is important because equipment is an essential part of the construction industry.
Contractors need reliable access to the tools they use to complete project-related tasks each day. When equipment isn’t available or isn’t working properly, tasks get delayed and safety may be compromised.
With effective equipment management, a business will be able to:
Better plan project schedules
Make informed purchasing decisions
Ensure the right tools are always available
Stay on top of repairs, maintenance, and leasing agreements
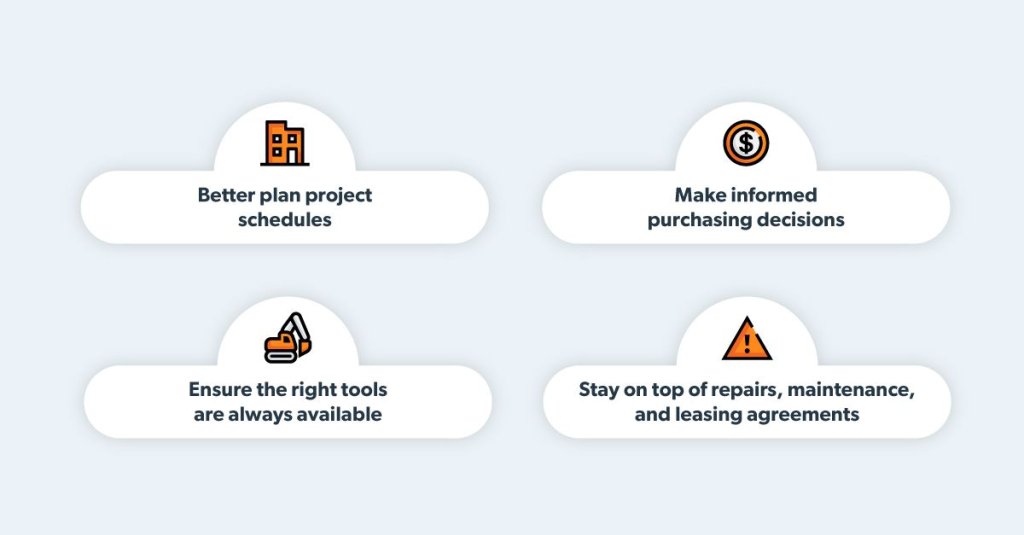
Better plan project schedules
A big part of equipment management is tracking the use of equipment in the field. When you have a clear, organized process for reporting equipment use, you can utilize data from past projects to accurately schedule similar work in the future.
Is your crew currently using a backhoe for a task that took 20 hours on a previous project? Don’t schedule any additional work using that equipment until the end of that timeframe. Or, are you making the schedule for a project that involves the use of multiple excavators? See how many were used for a similar task in the past to determine when you’ll have the right amount of resources available.
Recommended Read
The Importance of Project Timelines in Construction
Read about all the moving pieces to consider when planning a project schedule.
Make informed purchasing decisions
Whether you own or rent, construction equipment is a major expense. Tracking how you use equipment will help you understand exactly what you need—and how long you need it—so you can make informed decisions about buying or renting.
For example, your road construction team may frequently need to move large quantities of dirt using earth movers. With good equipment management practices, you can determine if there are opportunities to save time if more equipment is made available.
If you own your equipment, it may be time to add another asset to your fleet. And, if you rent, you may want to expand your contract.
Ensure the right tools are always available
Even with careful planning, you may run into extreme weather, safety and quality concerns, or other issues that cause project delays unrelated to equipment management. Sometimes because of these unexpected issues, certain equipment may be needed longer than anticipated.
In this case, you need a system in place to keep your crew informed and make changes to any affected project schedules as soon as possible.
Your construction equipment management plan should make it easy for you to quickly assess what equipment you have available and strategically reassign or reschedule.
Stay on top of repairs, inspections, and maintenance
Equipment management also includes monitoring equipment maintenance and inspection schedules. Keeping equipment properly maintained prevents safety concerns and helps your team stay productive.
You should also be able to track when equipment breaks and needs repairs. If a piece of equipment isn’t operational, your crew must be notified and kept aware of repair progress.
Finally, good equipment management also makes it easier to track rental or lease agreements. Make sure that information is easily accessible so you’re never in violation of your terms.
Common equipment management pitfalls
The most common mistakes construction companies make regarding equipment management are:
Having idle equipment
Mistimed maintenance
Rental contract disputes
Poor communication
Idle equipment
When equipment sits unused on the jobsite while it could be utilized on another task or project, money and time are wasted. This is especially true when you rent your construction equipment.
Most of the time, disorganization and miscommunication are to blame for idle equipment.
Most of the time, disorganization and miscommunication are to blame for idle equipment.
Mistimed maintenance
Another common mistake with construction equipment management is losing track of inspection and maintenance schedules.
Project schedules are often drafted well in advance. You need to know when you won’t have access to certain assets because of maintenance so you can plan work accordingly.
Rental contract disputes
Your equipment rental agreement may contain clauses about the proper use of equipment and responsibility for potential damages.
You put yourself at risk for disputes if you don’t closely monitor and report how you use rental equipment in the field. With an accurate record of equipment use, in the event of a dispute you can demonstrate you followed the terms of the contract as closely as possible.
Poor communication
Good communication helps prevent misunderstandings that lead to delays or safety issues.
If you don’t have a way to quickly and effectively communicate from the field to the office, stakeholders may remain unaware of needed repairs and other equipment concerns that could have been avoided or resolved immediately.
Recommended Read
3 Common Construction Equipment Mistakes (and How to Avoid Them)
Equipment can cause major cost overruns on any given project.
Equipment management best practices
Despite the common pitfalls, managing your equipment is easier with the help of smart tools and strategies.
The best practices for construction equipment management are:
Log use in detail
Track location
Store safely
Be proactive about maintenance
Use construction equipment management software
1. Log use in detail
To best understand the way your team works with equipment and protect yourself against any rental disputes, give your workers the tools they need to closely record equipment use in the field.
Track use hours, assign work to cost codes, and log idle times. Review field data frequently and assess how issues like weather or safety concerns affected equipment usage.
You can use these detailed insights to measure performance, prove compliance, and better plan future projects.
2. Track location
You should be able to definitively say where any part of your fleet is at any time.
Knowing your equipment’s exact location will help you make quick decisions when you need to schedule new work or reschedule current tasks.
3. Store safely
Make sure that when your team goes home for the day, they don’t leave your equipment vulnerable.
Avoid accidental damage, wear and tear, and theft by enforcing safe, secure storage procedures.
Recommended Read
Securing a Construction Site Toolbox Talk
Teach your crew how to secure the construction site from theft, vandalism, trespassing, and more.
4. Be proactive about maintenance
Don’t wait for the last second to comply with inspection and maintenance requirements. Familiarize yourself with the manufacturer’s specifications and be sure to schedule maintenance with plenty of time to spare before the asset is needed for work again.
Proactively keeping your assets in the best condition prevents delays from mistimed maintenance or unexpected breakdowns and ensures your crew is working with the safest, most reliable equipment possible.
5. Use construction equipment management software
It’s difficult to follow these best practices with pen and paper.
Construction equipment management software helps you stay organized without spending hours logging equipment use and sending notifications manually.
Make things easier on both the field and office by going digital.
Construction equipment management software
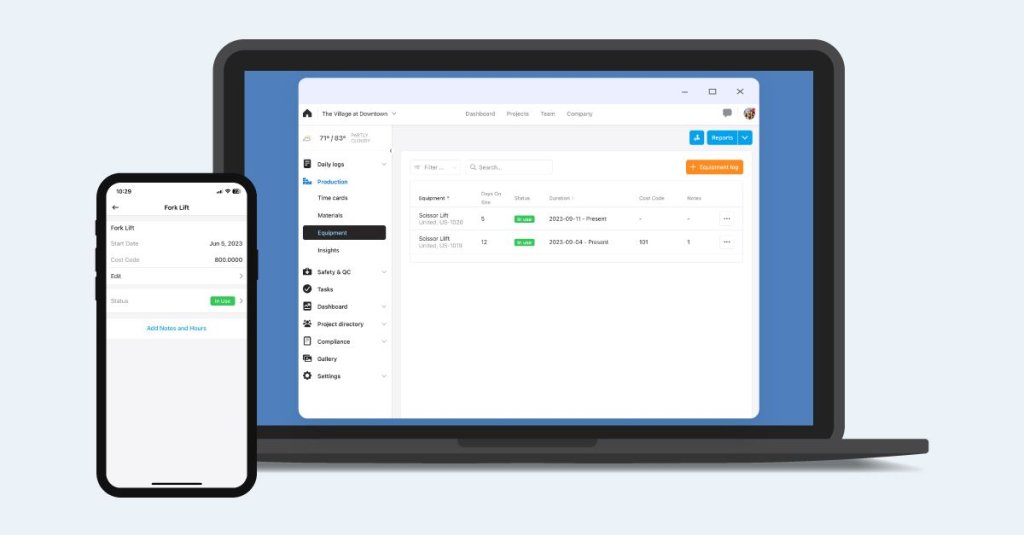
How does software streamline asset management in construction?
While different solutions offer unique advantages and disadvantages, the most effective equipment management software includes the following features.
Mobile data capture
Thanks to mobile data capture, your team can use their phones or tablets to quickly log equipment data on the go. Instead of having to record details on paper, they can use standardized templates that show where equipment is, what it’s being used for, and how many hours it is in use.
Some equipment management software features photo and video capabilities for even better visibility. They can snap time stamped photos of equipment so offsite stakeholders can visually verify location and condition.
Real-time data sharing
Software helps keep all stakeholders on the same page because it makes it easier to share field data about equipment use in real time.
Instead of having to collect and organize physical reports each day, you can view a digital copy as soon as it’s submitted. Just open a web portal or an app to see equipment status right at that moment.
Automated workflows
Let software do the hard work. When it’s time for maintenance, your software can automatically notify stakeholders with days—or weeks—to spare. It can also help you notify your team when equipment is or isn’t available as expected.
Equipment management software can automatically combine data from multiple reports into one, eliminating the need for manual data entry.
Some software may also include material and time tracking features. Using these along with equipment management, you’ll gain a complete picture of project performance.
In conclusion…
Properly managing your construction equipment helps your team work more efficiently and effectively. Because equipment is essential to the construction process, establishing an equipment management plan should be a high priority for every construction business.
Tools like construction equipment management software will help you manage your fleet in a streamlined way and prevent common pitfalls like idle time and poorly-timed maintenance.
We make equipment management easy
With Raken, keep all your important project information in the same place. Track use and see where your owned and rented equipment is at a glance for easy, accurate scheduling.